Glycolic acid 70% solution on produce method.
Description
Glycolic acid project adopts the production process of cyanide hydrolysis. Glycolonitrile is intermediate product of cyanide hydrolysis method. It is directly sourced from the Glycolonitrile production unit in the original plant area.
Directly using Glycolonitrile as a production raw material, it is low investment in production equipment, source of raw materials convenient and stable. It greatly reducing production costs, environmental risks and environmental impact.
Process
The raw materials stored in various storage tanks in the workshop by pipelines or tank. It is pumped into the reaction kettle of each section by gravity flow or pump metering.
Production materials
1. Glycolonitrile
2. Methanol
3. Sulfuric acid
4. Primary water
5. Ammonium hydroxide
1.Glycolonitrile Acid hydrolysis
Pour a certain amount of soft water into the hydrolysis kettle, while starting the stirring, slowly add concentrated sulfuric acid into the hydrolysis kettle, and then slowly drip Glycolonitrile into the hydrolysis kettle. During the drip process, control the temperature (110130C). After dripping, keep it warm for 8 hours.
Main Formula
HOCH2CN+H20+H2SO4→ HOCH2COOH + NH3
Sub Formula
HOCH2CN → HCNHO + HCN
HSO4+NH3 → NH4HSO4+(NH4)2SO4
2. Esterification
1) Dehydration: Turn on the condensate to cool down, and when the hydrolysate drops to the specified temperature (around 80~90 ℃), pump the feed liquid into the esterification tank. Turn on vacuum (not less than -0.090Mpa) and then turn on steam heating for reduced pressure dehydration. When the temperature reaches the dehydration end point (90~100 ℃), turn off steam to stop heating, turn on condensate to cool down, and when the temperature drops to the specified temperature (about 50~60 ℃), turn off vacuum and prepare for esterification.
2) Primary esterification: In the first batch, when the cooling of the feed liquid (50~60 ℃) is completed, 98% methanol is added, and then heated and refluxed for 2h (For the second batch and subsequent batches, apply salt washing alcohol and residue, add the previous batch of salt washing alcohol to the feed liquid of the esterification tank instead of new alcohol, while adding the residue, heat up and reflux for 2h.).
HOCH2COOH+H2COH → HOCH2COOCH3+H2O
3) Demineralization: After the primary esterification is completed, turn off the steam and turn on the condensate to cool the feed liquid to about 30~40 ℃. Place the esterification feed liquid in the suction tank and press to remove salt. After the filtrate has been drained, it is returned to the esterification tank for distillation.
4) Distillation: Primary distillation: After the cooling of the feed liquid (about 30-40 ℃) is completed, start the vacuum pump and perform reduced pressure distillation (vacuum degree not less than -0.095Mpa). When the temperature of the feed liquid rises to the specified temperature (90-100 ℃), turn off the steam and stop heating. When the fraction is no longer distillable, turn off the vacuum and turn on the condensate for cooling. After metering the fraction distilled under reduced pressure, transfer it to Methyl glycolate hydrolysis tank, and the primary distillation is completed. Secondary esterification: When the cooling of the feed liquid after the primary distillation (50-60 ℃) is completed, add methanol. Turn off the condensed water and turn on the steam for heating and refluxing for 1h.
Secondary distillation: The specific process is synchronized with a single distillation. Put the residue in the esterification tank into a bucket and measure it. If the residue is large, it needs to be esterified three times. If there is a small amount of residue, store it in a sealed container and prepare for insertion into the next batch.
5)Methyl glycolate Hydrolysis :
After metering the fraction distilled under reduced pressure, pour it into methyl glycolate hydrolysis tank and add soft water to the hydrolysis tank. Start the steam to heat up. When the temperature is higher than 100 ℃, it is necessary to add water to the hydrolysis tank and heat preservation hydrolysis for 3h. During hydrolysis, methanol is vaporized and condensed, and the collected alcohol is metered and placed in the recovered alcohol storage tank.
HOCH2COOCH3+H2O → HOCH2OOH+CH3OH
6) Concentration: Start the vacuum pump of the concentration tank, filter methyl glycolate hydrolysate and pump it into the concentration tank. Start steam heating for reduced pressure concentration (vacuum degree not less than -0.095Mpa). At the end of temperature rise (50~60 ℃), turn off the steam and turn on the condensate to cool down, and stop concentration. Finally, glycolic acid 70% liquid is obtained.
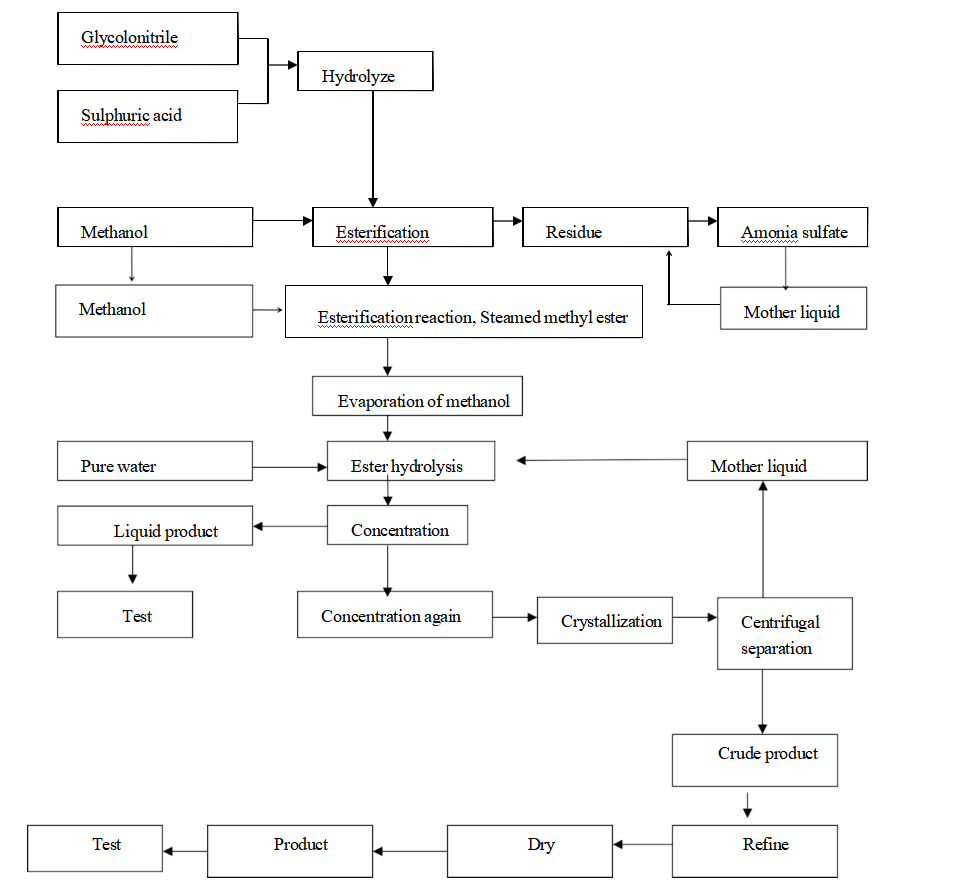